In the first half of this year, the National Group Standards Information Platform announced the "Contamination Control Strategy for Sterile Drug Production ( CCS ) Technical Guidelines" ( T/CPAPE 01-2024 ) organized by the China Pharmaceutical Equipment Engineering Association . This guideline was released in September 2023 . A draft for comments was released on June 7 and solicited opinions from the public. It has now been officially implemented on June 1 , 2024 . Although this guideline is not mandatory, it provides technical reference for pharmaceutical production and R&D enterprises, factory facility design units, equipment manufacturers, etc., and plays an important guiding role in improving pollution control in the pharmaceutical production process.
The rise of the concept of Contamination Control Strategy ( CCS ) is not accidental. It is an inevitable choice for generations of medical people to pursue drug quality ...
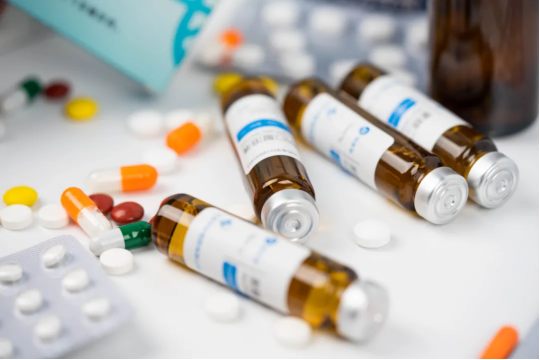
Where does the Contamination Control Strategy ( CCS ) come from?
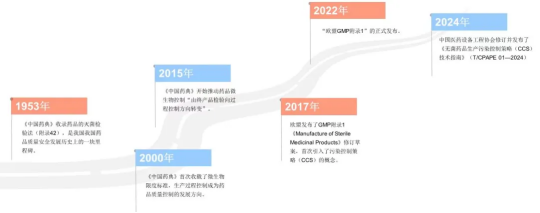
Where does the Contamination Control Strategy ( CCS ) come from?
Ensuring the quality of medicines is a major concern for the country and fundamental to the people. Due to their particularity, sterile drugs have become the focus of regulatory authorities at all levels in the industry. As early as the 1953 edition of the "Pharmacopoeia of the People's Republic of China" ( referred to as "Chinese Pharmacopoeia" ) , the sterilization test method of drugs was included (Appendix 42 ). The appendix points out that the sterilization test of drugs refers to testing whether the sterilization of drugs is complete. Specifically, Including sterilization testing methods for liquid drugs and sterilization testing methods for solid drugs. The implementation of this final product sterilization inspection method is a milestone in the history of the development of drug quality and safety in my country.
However, this inspection method also has certain limitations, such as the inability to achieve 100% inspection, complex inspection methods, high scrap rate, high cost, etc. Therefore, after decades of precipitation, the 2000 edition of the "Chinese Pharmacopoeia" finally included microbial limit standards. People gradually realized that the control of drug contaminating microorganisms is an important measure to ensure the safety of drugs, and production process control It is the development direction of pharmaceutical quality control. The 2015 edition of the Chinese Pharmacopoeia began to promote the " shift from final product inspection to process control " in drug microbial control [1] . This concept has continued to this day, and the quality control of sterile drugs has gradually shifted from " post-event control " to " pre-event and during-event control " .
The real breakthrough came in December 2017 , when the EU released a revised draft of GMP Annex 1 " Manufacturing of Sterile Medicinal Products" (referred to as " EU GMP Annex 1" ), the concept of Contamination Control Strategy ( CCS )* ** appeared and was officially confirmed with the release of " EU GMP Appendix 1 " on August 22 , 2022 . At the same time, the concept of parametric release has also appeared in the public eye. As implementation conditions continue to mature, sterile drug production process control will further move from detection to process control and parameter release.
What exactly is a Contamination Control Strategy ( CCS )?
" EU GMP Annex 1" has a clear definition of pollution control strategy ( CCS ) [2] :
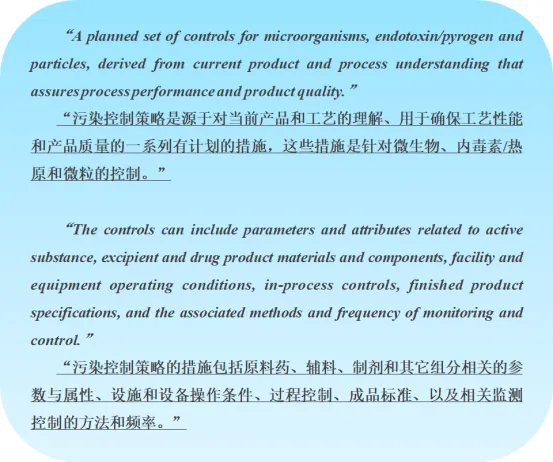
The applicable scope of pollution control strategy ( CCS ) is defined by relevant agencies as follows [3][4][5] :
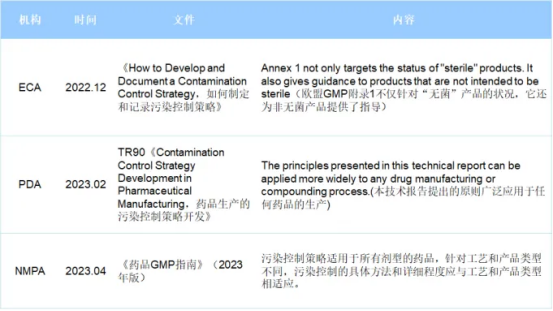
Why Care About Contamination Control Strategies ( CCS )
The essence of the Contamination Control Strategy ( CCS ) is to control possible contamination risks in all aspects of the pharmaceutical production process, and to remove / reduce / prevent contamination risks through scientific and systematic measures as much as possible, so as to ensure that enterprises can produce high-quality, safe and reliable products. products. Once pollution occurs, it will not only cause a waste of materials, but also require detailed investigation and rectification of pollution sources, which is time-consuming and labor-intensive, and will result in a huge loss; at worst, it will be investigated and dealt with by regulatory authorities, and even market recalls, which is very harmful to the enterprise. It's even more unbearable.
Now that the overall environment of the domestic pharmaceutical industry is declining, whether companies choose to continue to compete domestically or seek "overseas" development, they need to improve the competitiveness and compliance of their products. Implementing a pollution control strategy ( CCS ) is an important way to improve product competitiveness and compliance. Especially for companies seeking to "go overseas", it is even more necessary to strictly benchmark relevant international laws and regulations, such as "EU GMP Appendix 1 ", etc. and strictly enforce it.
If an enterprise wants to implement a pollution control strategy ( CCS ), it needs to have a detailed understanding of the entire production process of its products, including but not limited to factory facilities, equipment, personnel, public systems, materials, products and processes, environmental monitoring, suppliers, etc. wait. These factors interact and are interdependent. When evaluating and formulating a pollution control strategy ( CCS ), the overall impact of all factors on pollution risks needs to be comprehensively considered, which is a major challenge for enterprises.
Typical steps for developing and maintaining a pollution control strategy are as follows:
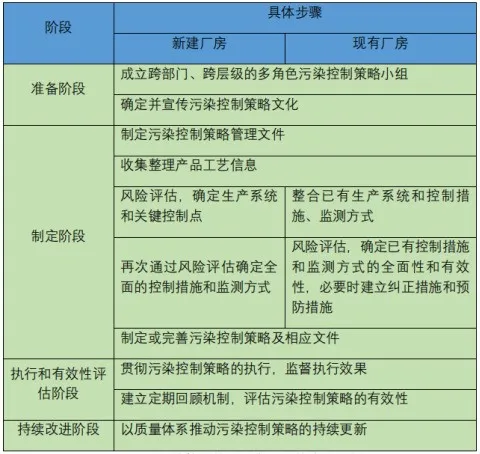
Examples of steps to develop and maintain a pollution control strategy
Based on this, it is not difficult to see that the Contamination Control Strategy ( CCS ) is an inevitable requirement to comply with the development of domestic and foreign industries. If relevant pharmaceutical companies want to maintain compliance and competitiveness, they must be aware of the formulation of the Contamination Control Strategy ( CCS ) And maintenance is a dynamic and continuous process. If you want to always be in line with international standards, you need to incorporate the pollution control strategy ( CCS ) into the company's own quality system, make corresponding records, output relevant documents, and summarize and update regularly.
Control elements of a pollution control strategy ( CCS )
Factory facilities
Factory facilities are a necessary guarantee for the quality of pharmaceutical production. Pharmaceutical manufacturers need to organize professional and technical personnel to plan and design factory facilities according to the requirements of different pharmaceutical dosage forms, and perform relevant verifications to confirm that their performance can meet expected needs. In the life cycle of factory facilities, good design alone is not enough. Its use, maintenance, repair and daily monitoring are also indispensable links. At the same time, factory facilities also need to be reviewed regularly to ensure that they can continue to operate effectively. Carry out pollution control. The formulation of pollution control strategies is inseparable from the overall consideration of the entire life cycle of factory buildings and facilities.
Taking a clean room as an example, the choice of decorative materials is directly related to the cleanliness, safety, durability and operating costs of the clean room. In view of the widespread application of hydrogen peroxide ( VHP ) disinfection method in clean rooms, higher requirements have been placed on the corrosion resistance of clean room partitions . As a supplier of clean room / laboratory decoration assembly solutions, United Pharma has launched United Pharma Zhenkang® anti - VHP color steel plate in response to this demand. After United Pharma's rigorous internal testing and customer field verification, this product has demonstrated significant advantages:
§The surface coating thickness of United Pharma Zhenkang® anti - VHP color steel plate is up to ≥150μm , far exceeding that of ordinary pre-roller coated color steel plate ( PPGI ), showing excellent hydrogen peroxide resistance. Moreover, compared with pre-roller coated fluorocarbon coating (PVDF) and polyester coating (PE) , United Pharma Zhenkang® anti - VHP color steel plate performs better in performance.
§Compared with SS304 stainless steel, United Pharma Zhenkang® anti - VHP color steel plate not only avoids visual fatigue, but its easy-care characteristics also greatly reduce maintenance costs, and is more affordable in terms of price, providing users with a cost-effective choose.
§equipment
§Equipment management includes all activities at each stage of the entire life cycle of equipment. An effective equipment management system can prevent and control potential contamination in the pharmaceutical production process to the greatest extent. Equipment design, use, maintenance and repair, and regular reviews are all key points of pollution control strategy. Insufficient control of any factor or lack of connection between factors may lead to defects in the entire pollution control strategy.
§
§personnel
§ Regarding personnel in the production of sterile drugs, it can be considered from the aspects of authority control, personnel hygiene and health conditions, clean clothing and changing process, training, clothing changing qualification certification, maximum number of personnel, clean clothing monitoring, clothing changing qualification re-certification, personnel qualifications The revocation and aseptic practices require these ten aspects to take preventive measures to minimize the contamination of facilities and products by microorganisms, pyrogens / endotoxins and particles.
§
§Public system
§The scope of clean public systems includes purified water, water for injection, pure steam and clean gas systems. Before designing a clean public system, each system needs a user requirement to define the user's requirements. The design will be designed accordingly based on user needs to ensure that the needs are met. After the design is completed, all plant facilities, systems and equipment must be confirmed to ensure that they are well installed, operating properly and producing expected results.
§
§ The public system is the basis for the production of sterile drugs. In order to prevent the introduction of relevant contamination into the public system during use, it is necessary to conduct targeted periodic quality monitoring of the system, complete regular maintenance plans, establish a regular system quality review mechanism, and form a corresponding Data analysis and trend reports (such as monthly, annual reports). In addition to daily normal use, for some planned shutdown maintenance or shutdown after encountering abnormal conditions, enterprises should formulate relevant shutdown and recovery procedures to avoid pollution to the maximum extent.
§
§materials
§ Throughout the product life cycle, materials (including raw materials and primary packaging materials) should also be effectively controlled in each process / step based on risk assessment.
products and processes
For different products and processes, such as aseptic production process, terminal sterilization process, freeze-drying process, BFS process, FFS process, etc., it is necessary to design a set of pollution control strategies that meet the product characteristics based on the focus of the process. ( CCS ). In summary, any risks and requirements associated with aseptic processing should be identified, assessed and appropriately controlled.
Take the filling process of sterile preparations as an example, which involves multiple steps such as equipment cleaning, disinfection, filling, and sealing. In this process, small mistakes in any step may lead to contamination of the medicine. For example, when disassembling and assembling filling pipelines and filling pumps, some current filling methods are difficult to close the door and require tedious aseptic and cleaning operations, which poses challenges to the sterility assurance of key areas. In response to this, Zixian Technology has launched a pumpless filling system, which has outstanding performance in simplifying aseptic operations, improving filling accuracy, controlling dripping and splashing, and reducing shear damage:
§The pipeline design of this system achieves complete visualization. The working pump tube is cleverly placed between two movable rollers and adopts automatic cone positioning, which greatly simplifies the installation and disassembly process. The operation process of pipeline replacement only requires It takes 8 minutes. Compared with ceramic pumps, the operating time can be reduced by 73% , significantly reducing the risk of bacterial contamination in manual operations and the time required for equipment maintenance.
§ This system only connects the dispenser and the filling needle through a hose. The valve-less design in the middle completely eliminates sanitary dead corners. During the transfer process, the liquid will not come into contact with other parts except the hose and the 316L connector. Any media contact greatly avoids the risk of cross-contamination and sterile contamination.
§ ......
It is reported that Zhixian Technology has reached in-depth cooperation with many large enterprises such as Qilu Group, Beijing Sinovac, Lunan Group, Simcere Pharmaceuticals, Livzon Group, and Renfu Group, and has been highly recognized by customers.
environment
The starting point of environmental monitoring requirements is based on requirements such as regulations or pharmacopoeias. The characteristics of the product and its process steps determine the required production environment level, but it is not a control measure in itself. By confirming whether the environment meets the requirements of regulations, providing effective feedback on pollution control measures, and identifying potential sources of pollution, the purpose of continuously improving control measures can be achieved.
At the same time, although environmental monitoring is an effective way to reflect the level of environmental pollution, the variability of the monitoring method itself is relatively high. Enterprises need to realize that the level of sterility assurance does not rely on environmental monitoring and aseptic process simulation detection. Environmental monitoring data are more about identifying changes in environmental controls than providing quantitative information on environmental microbial and particle levels.
In general, since the National Medical Products Administration ( NMPA ) gradually joined ICH and became an official applicant for PIC/S , domestic pharmaceutical laws and regulations have further aligned with international standards, and with this has come an increase in China's GMP inspection standards. , coordination of inspection standards and strengthening of regulatory forces. Regardless of whether domestic pharmaceutical companies are producing and selling locally or exporting overseas, establishing a complete pollution control strategy ( CCS ) system is a necessary measure to cope with domestic and foreign supervision and improve the quality of the company's products.
References
[1] Hu Changqin . Current status and prospects of pharmaceutical microbial control system construction [J]. Chinese Modern Applied Pharmacy , 2021, 38(5): 513-519.
[2] " Manufacture of Sterile Medicinal Products , Sterile Pharmaceutical Production"
[3] " How to Develop and Document a Contamination Control Strategy"
[4] TR90 " Contamination Control Strategy Development in Pharmaceutical Manufacturing , Contamination Control Strategy Development in Pharmaceutical Manufacturing"
[5] " GMP Guidelines for Drugs" ( 2023 Edition)
[6] "Technical Guidelines for Contamination Control Strategies ( CCS ) for Sterile Pharmaceutical Production "